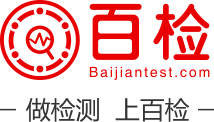
钢水炉外精炼就是将炼钢炉中初炼的钢水移到钢包或其他专用容器中进行精炼,也称为二次精炼。在真空、惰性气氛或可控气氛的条件下进行深脱碳、脱硫、脱氧、除气、调整成分(微合金化)和调整温度并使其均匀化,去除夹
钢
水炉外精炼就是将炼钢炉中初炼的钢水移到钢包或其他专用容器中进行精炼,也称为二次精炼。
在真空、惰性气氛或可控气氛的条件下进行深
脱碳
、
脱硫
、脱氧、除气、
调整
成分(微
合金化
)和调整温度并使其均匀化,去除
夹杂物
,改变夹杂物形态和组成等。钢水炉外精炼是为适应钢的
品种
质量的提高,
生产
新钢种以及生产过程合理化,为连铸对钢水成分、温度、纯净度和时间等衔接的严格要求,不可缺少的
工序
,成为现代炼钢、连铸生产中的重要环节。为了创造*佳的
冶金
反应条件,到目前为止,炉外精炼的基本手段有搅拌、渣洗、加
热
、真空、喷吹等5种。实际生产中可根据不同的目的选用一种或几种手段组合的炉外精炼技术来完成所要求的精炼任务。
(1)钢种的质量要求;
(2)连铸机生产对钢水的质量要求;
(3)
转炉
与连铸机生产的
作业
协调要求。
选择炉外精炼
工艺
,应考虑
产量
(及炉子容量)、钢的质量、钢种的特性以及采用炉外精炼的
经济
效果,其中尤以适应钢的质量要求为首要目的。有的炼钢车间为了适应多种钢的
需要
甚至设有两种或两种以上的炉外精炼设备。
1.渣洗:将事先配好(在专门炼渣炉中
熔炼
)的合成渣倒入钢包内,
借
出钢时钢流的冲击作用,使钢液与合成渣充分混合,从而完成脱氧、脱硫和去除夹杂等精炼任务。
2.真空:将钢液置于真空室内,由于真空作用使反应向生成气相方向移动,达到脱气、脱氧、脱
碳
等目的。真空是炉外精炼中广泛应用的一种手段。
3.搅拌:搅拌方法:吹气搅拌和
电磁
搅拌。
4.加热:加热方法:电弧加热法和化学加热法。
5.喷吹:用气体作载体将反应剂加入
金属
液内的一种手段。喷吹的冶
金
功能取决于
精炼剂
的种类,它能完成脱碳、脱硫、脱氧、
合金
化和
控制
夹杂物形态等精炼任务。
6.
过滤
、喂线
精炼设备与工艺能够完成的冶金功能可概括为:
脱气(脱氢、脱氮),脱氧,脱硫,清洁钢液(减少
非金属
夹杂物,提高显微清洁度),脱碳(冶炼
低碳
、超
低碳钢
种),真空碳脱氧,调整钢液成分(微调与均匀*终化学成分),调整钢液温度。
炉外精炼方法的选择应满足产
品质
量的要求,不同
产品
对炉外精炼的功能有不同要求。
1.
厚板
:脱氢、脱硫、减少氧化物夹杂
2.
钢轨
:脱氢
3.轮箍:脱氢、去除夹杂物
4.
薄板
:脱碳、脱氧
5.
管材
:脱硫、减少氧化物夹杂
6.
轴承钢
:脱氧、减少氧化物夹杂物、脱硫、改变
硫化物
形态
7.
不锈钢
:脱碳保
铬
、脱氢、减少夹杂物、降低
成本
炉外精炼的另一个积*意义是减轻炼钢炉的负荷,提高其生产力。比如采用连铸的转炉车间,尤其是全连铸车间,往往都选用LF或其他加热型精炼装置。
钢包吹氩搅拌是*基本也是*普通的炉外处理工艺。
(1)均匀钢水温度。从炼钢炉流到钢包的钢水,在钢包内的温度分布是不均匀的。由于包衬吸热
和钢
包表面
散热
,包衬周围钢水温度较低,中心区域温度较高,钢包上、下部钢水温度较低,而中间温度较高,这种温度差异导致中间包浇注过程钢水温度前后期低,中期高。钢包吹氩搅拌促使钢
包钢
水温度均匀,并且能使钢水向包衬的传热进入稳定态,这样连铸过程钢水温度稳定均匀,有利于提高铸坯内部质量,使结晶器内坯壳生长均匀,避免开浇
水口
冻钢断流。
(2)均匀钢水成分。出钢时在钢包内加入大量的
铁合金
,成分不均匀,吹氩搅拌可使钢水成分均匀。在出钢过程就可开始吹氩搅拌。在吹氩搅拌过程中可根据快速分析提供的钢水成分而进行成分微调,以使钢的成分控制
范
围更窄,以确保
钢材
性能均匀。
(3)促使夹杂物上浮。搅动的钢水促进了钢
中非
金属夹杂物碰撞长大,上浮的氩
气泡
能够吸收钢中的气体,同时粘附悬浮于钢水中的夹杂物并带至钢
水表
面被渣层所吸收。生产实践表明,吹氩搅拌后钢水氧含量有明显降低,其降低幅度与脱氧程度有关,一般可降低20%以上;但脱氮效果不明显,并要注意减少增氮。对w[Al]<0.01%的钢,吹氩搅拌可降低夹杂物含量25%以上,对w[Al]>0.02%的钢,吹氩搅拌可降低夹杂物含量约55%。吹氩搅拌排除的夹杂物数量与钢水液面上覆盖渣层FeO含量有关,渣中的FeO含量越低,吹氩搅拌夹杂物排除的量越多。
钢包吹氩,通常有两种形式如下:
(1)底吹氩。底吹氩大多数是通过安装在钢包
底部
一
定位
置的透气砖吹入氩气。这种方法的优点是均匀钢水温度、成分和去除夹杂物的效果好,设备简单,操作灵便,不需占用固定操作场地,可在出钢过程或
运输
途中吹氩。钢包底吹氩搅拌还可与其他技术配套组成新的炉外精炼方式。缺点是透气砖有时易堵塞,与钢包寿命不同步。
(2)顶吹氩。顶吹氩是通过吹氩枪从钢包上部浸入钢水进行吹氩搅拌,要求设立固定吹氩站,该法操作稳定也可喷吹粉剂。但顶吹氩搅拌效果不如底吹氩好。
吹气位置不同会影响搅拌效果,水力学模型和生产实践都表明,吹气点*佳位置通常应当在包底半径方向(离包底中心)的1/2~2/3处;此处上升的气泡流会引起
水平
方向的冲击力,从而促进钢水的循环流动,减少涡流区,缩短了混匀时间,同时
钢渣
乳化程度低,有利于钢水成分、温度的均匀及夹杂物的排除。钢包中心底吹气有利于钢包顶渣和钢水的反应,脱硫效果好。以均匀钢水温度和成分为主要目的的吹氩搅拌,吹气点应偏离包底中心位置为好。总的来说,底吹氩位置,应根据钢包处理的目的来决定。对顶吹氩而言,吹氩枪插入越深,搅拌效果越好。
钢包吹氩用压力、流量随着钢包容量的增大而加大。
工作
压力、流量确定的一般原则是:*小值的设定应确保透气砖或吹氩枪不被堵塞;*大值则以钢包液面渣层不被大面积吹开,以免钢水二次氧化。采用较大的吹氩流量,叫强搅拌。预吹氩、加
废钢
调温或调合金时采用强搅拌,以加速废钢、合金
熔化
,充分混合,
保证
钢水成分、温度均匀。其后的时间应采用较小的吹氩流量进行弱搅拌,以促进夹杂物上浮,净化钢水。经过小流量较平稳的弱搅拌,抑制了顶渣卷混、二次氧化等现象,氧化物夹杂总
量比
吹氩处理前可大幅度降低,一般降低量可达45%,大于20μm的夹杂物可从钢水中被分离去除,因此要净化钢水,必须保证有足够的弱吹氩时间。
此外,需要脱硫时,则要用更大吹氩流量进行强搅拌,加速渣钢
界面
反应以利于脱硫。
惰性气体中的氩气,不溶解于钢水,也不与任何元素发生反应,是一种十分理想的搅拌气源,因此被普遍采用。从搅拌作用而言,氮气与氩气一样,且氮气便宜,但在高温下氮能溶解在钢水中,其增氮量是随温度的升高及吹氮时间的延长而增多。当温度高于1575℃时,可使钢中氮含量增加0.003%,影响钢的质量,因而使用氮气作为搅拌气源受到了限制,仅有少量含氮钢种可用吹氮气搅拌,但还存在增氮不稳定的问题。